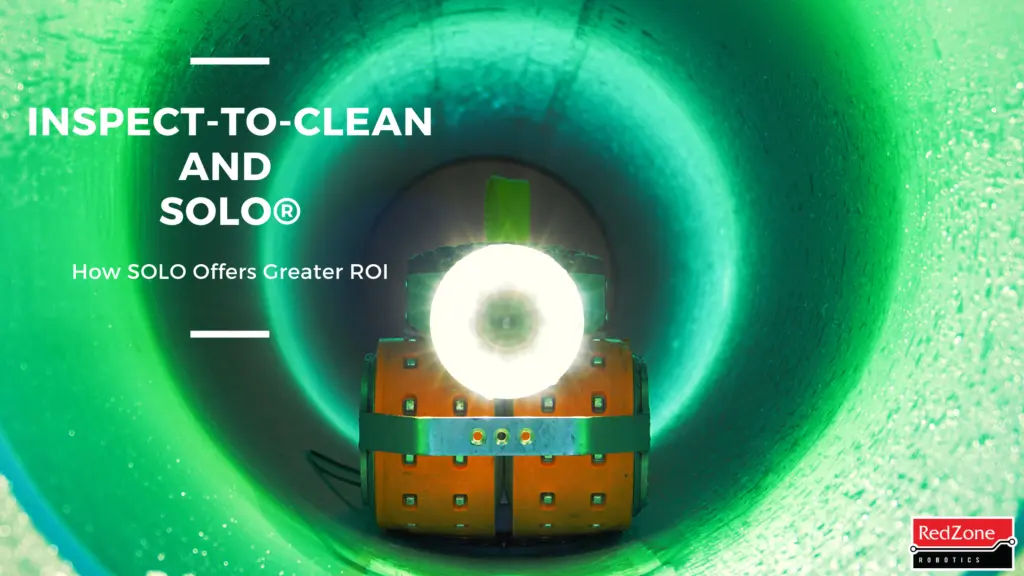
As the water and wastewater industries continue to develop new advancements in technologies and equipment, it is also important to look at how current processes can be improved by changing our approach. In order to make decisions that improve efficiencies or create a greater ROI, we have to look at the data, letting it drive our decisions and directions.
The SOLO® robot has already changed sewer system evaluations. With its autonomy and 360-degree video, utilities and system owners are able to inspect their system in record time. Additionally, creating these baseline assessments for the entire system now helps prioritize maintenance for the most severe defects or pipes. It has the ability to collect ample amounts of inspection data, and the post-processing can increase the speed and quality of QA/QC. This is the foundation for any asset management program. But what else can all of this this data be utilized for?
Using data to improve processes
RedZone sought to answer this question by looking at the history of SOLO® inspections. To date, RedZone has completed over 75 million linear feet of inspection across all platforms, with a significant portion completed by the SOLO® autonomous robot. This is due to the speed of collection mentioned above, and due to the fact that many collections systems are comprised of a majority of pipes less than 12-inches. Surely, there must be something this data can tell us about our approach to inspection.
Taking a subset of 30 million feet of 8-12-inch inspections from the period of 2010-2018*, RedZone analyzed the types of defects and success rate of the SOLO® units. This included looking at NASSCO Pipeline Assessment Certification Program (PACP) codes, the standard in North America for grading and characterizing deficiencies within a pipe. More specifically, this identified inspections that were marked by an ‘MSA’ – a code for an abandoned survey, or an assessment that cannot be completed. This is usually due to an obstruction or blockage that impedes the robot. These defects can lead to significant issues within a collection system, such as pipe failures, infiltration, and overflows.
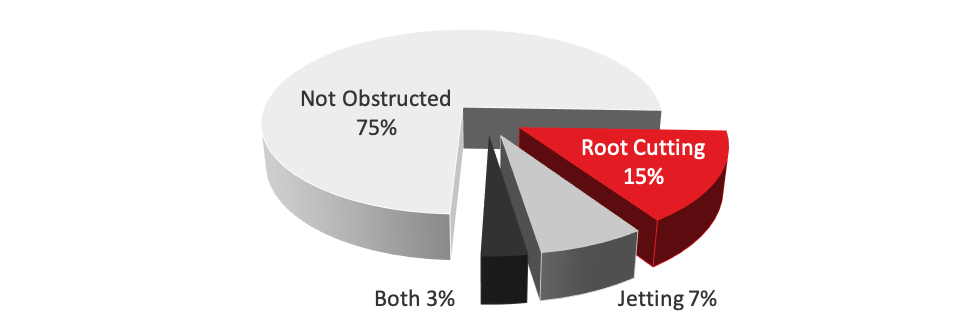
The data indicates that the SOLO® units were able to successfully complete 75% of the inspections in as-is conditions, meaning pipes that were not pre-cleaned. This shows that a large subset of the pipes could still successfully be inspected and traversed without jetting; breaking the notion that ‘all wastewater pipes require cleaning’. Furthermore, this analysis shows that the defects that halted inspection were not likely to be corrected by pre-cleaning. Many of the obstacles were roots or intruding taps, which require other methods for correction. It’s important to note that many of these defects would not have been found unless a CCTV inspection had occurred initially.
Why clean first? Inspect-to-clean saves time and money.
The inspect-to-clean approach, provides a greater ROI for a system owner. Using a fast and efficient camera the most severe defects and issues within a system can be identified. Saving on pre-cleaning costs for ~75% of the system allows crews to be focused on where they will make the most impact. It should be noted that camera units will still run into defects and obstructions within the pipelines, however, knowing the specifics of the defect via inspection allows for better decision-making for a solution. This is how prioritization for asset management should work!
What else can we learn?
When the data is separated by year, we begin to notice an interesting, but logical, trend. It shows that as the years progress, the percentage of the system that can be completed without the need to be cleaned actually goes down. This is easily explainable — the longer you wait to complete an inspection or resolve an issue, the more likely it is to become a problem. This demonstrates the need for preventative maintenance via a routine inspection program for identifying problems. The return on investment for an inspect-to-clean approach is still viable, but waiting is no longer an option.
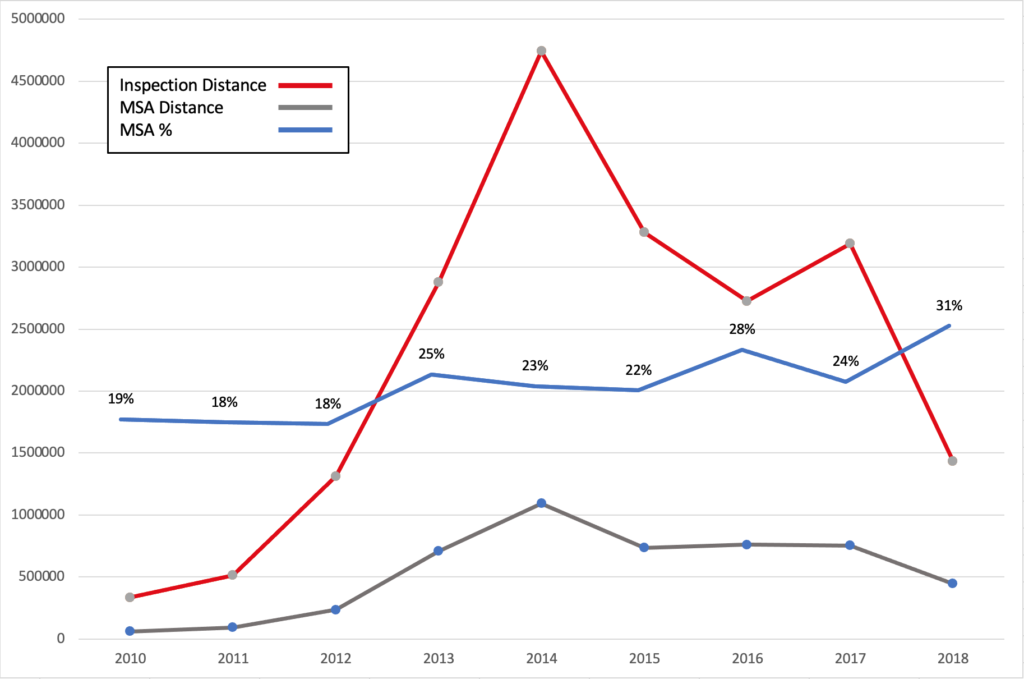
RedZone continues to use its advanced technology and data analytics to better improve utilities. The SOLO® robot is a perfect example: capable of efficient inspections through autonomy and using its vast inspection history to identify a unique approach. When it comes to creating a baseline inspection and informing an asset management plan for years to come, SOLO is the ideal solution.
*Data is comprised of metadata from the inspection and includes no spatial or location-based identifying information.
Want to learn more about inspect-to-clean services? Get the case study here.