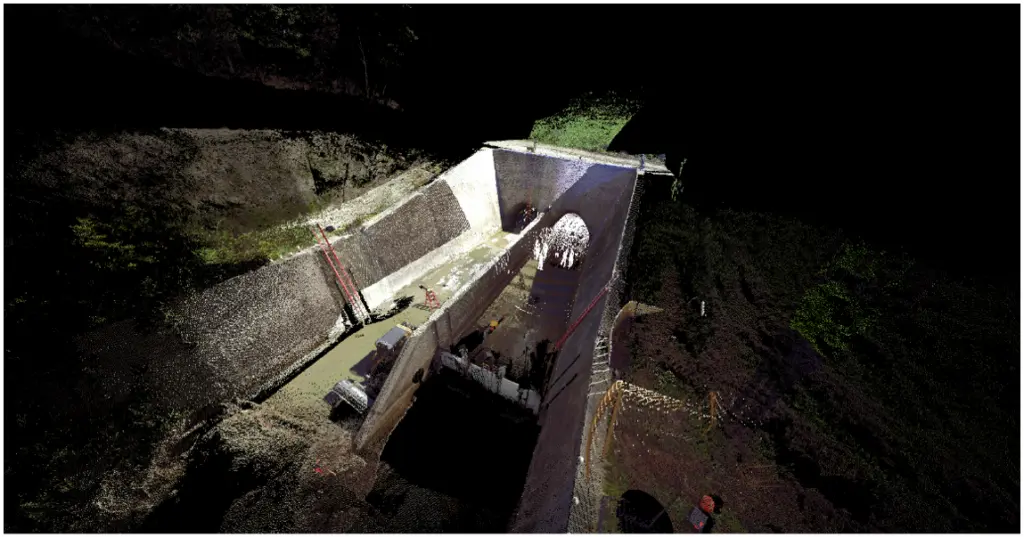
As the pioneers of multi-sensor inspection (MSI) for advanced pipeline assessment, RedZone Robotics has a rich, storied history with robotics and sensor technology.
With MSI, two of the most misunderstood concepts are differentiation between LASER and LiDAR technologies, and collection and interpretation of 2D versus 3D data. The two are fundamentally different. But, in what ways? And how do the technologies actually work?
In this article, we’ll explore the sensor technology options while discussing the best use cases and methodology associated with each type.
Let’s break it down.
What is LASER?
A LASER is a device or technology capable of converting light or electrical energy into a focused, high-energy beam.
Laser light is monochromatic (single light frequency – i.e., one color). And, although the beam can travel long distances, it diverges and becomes less accurate.
While the foundation of Light Amplification by Simulated Emission of Radiation (LASER) technology dates back to Albert Einstein’s prediction of “stimulated emission” back in 1917, it wasn’t until 1960 that Theodore Maiman built the first working laser prototype while working with the Hughes Aircraft Company. Maiman’s laser used synthetic ruby for military range finders, and is still used commercially for drilling holes in diamonds due to its high peak power.
With regards to advanced pipeline assessment, the term “laser” is often used synonymously with “ring laser,” “laser profiling,” or “structured light” inspections. In essence, a laser light (beam, ring, etc.) is projected onto the interior wall of a pipe surface, and a separate camera is used to record the image of the light ring.
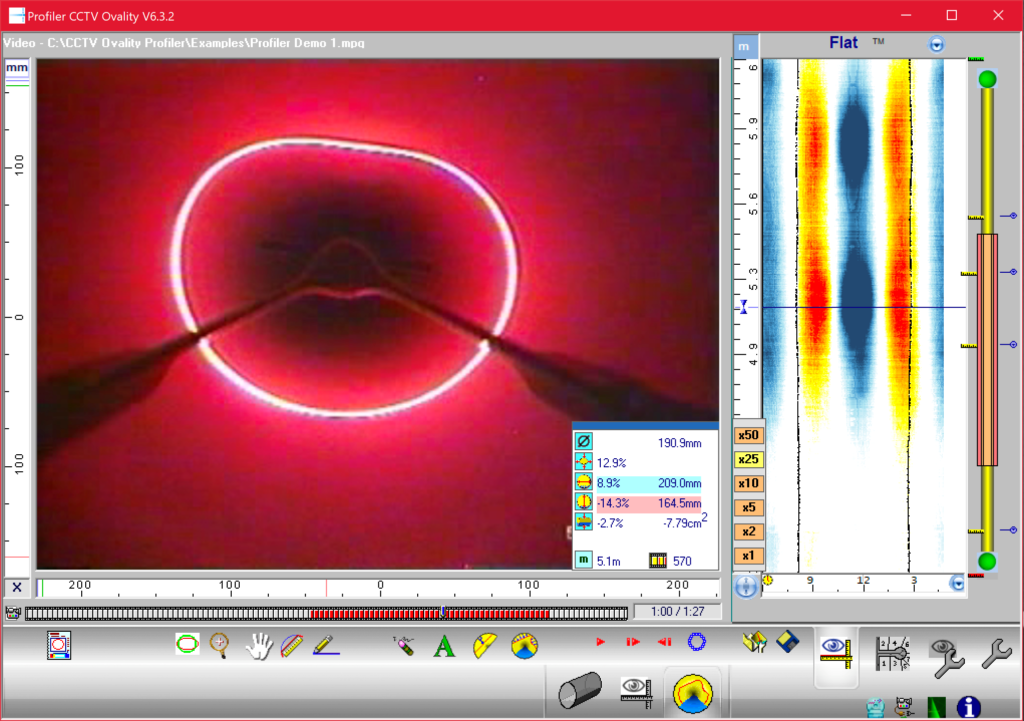
What is LiDAR?
Light Detection and Ranging (LiDAR) is a remote sensing methodology that measures distances to objects by illuminating the target with lasers, then analyzing the reflected light.
Unlike LASER, which is a technology, LiDAR is a methodology…one which employs the use of lasers.
A year after Hughes Aircraft Company built the first laser, in 1961, they developed the first LiDAR prototype. Though, it wasn’t until the mid-1980s, when GPS satellite communication reached its full configuration, that LiDAR become more precise, and thus, more widely used.
As it pertains to MSI, LiDAR is functionally similar to sonar techniques, in that the time of flight (TOF) or propagation time of the echo is the distance between the sensor and the target.
LIDAR utilizes LASER technology, but vice versa is not true. Besides TOF, LiDAR sensors can be placed in Doppler (laser phase shifts) or Geiger (laser energy) modes to estimate ranges (distances).
You can read more about LiDAR here.
Which is more accurate for a pipeline inspection?
Accuracy depends on the size of the pipe diameter being measured.
Ring lasers have stated inaccuracies that are a percentage of the distance being measured (e.g., +/- 0.5%), which is most often a function of the resolution of the camera capturing the laser image.
LiDAR sensors have internal processors with stated inaccuracies that are fixed across the useful distance of the sensor (e.g., +/- 30mm).
In essence, ring lasers are more accurate in small to medium sized pipes, and LiDAR is more accurate in larger pipes.
2D vs. 3D Laser Inspection – What’s the Difference?
As the name implies, 2D sensors use a single plane of lasers to capture X and Y dimensions.
This could be accomplished with a continuous ring of projected light or a single spinning laser beam. Either way, ring lasers and 2D LiDAR sensors collect the same type of X and Y dimensional data.
The movement of the sensors down a pipe facilitate collection of successive 2D data slices, which are often presented in 3D formats. This can be misleading and should not be confused with true 3D LiDAR.
Bottom Line: 2D sensors are most suitable for performing detection and ranging tasks.
As for 3D LiDAR sensors, they function like their 2D counterparts. However, they also take additional measurements along the Z-axis to collect real 3D data. The third axis data collection is most often accomplished with multiple lasers at varying angles or lines of vertical projection.
Modern laser projection and wide-area scanning technologies allow highly accurate, high resolution 3D data to be collected without blind spots. However, this type of data collection comes with a cost: money and time.
3D sensors are significantly more expensive than their 2D counterparts. Also, traditional 3D LiDAR scanners must remain steady and stable during data acquisition, and data processing is inherently more complicated.
Thus, the time required to collect and process 3D LiDAR data during an advanced pipeline inspection leads to a major increase in overall cost.
Bottom Line: 3D LiDAR is most suitable for mapping and detailed analysis, such as bend radius, to be used for engineered designs.
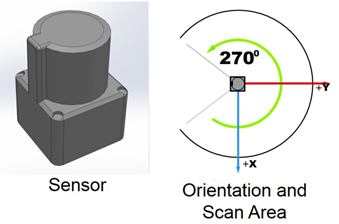
Sample 2D LiDAR sensor and range (courtesy Hokuyo Automatic Co., LTD.)
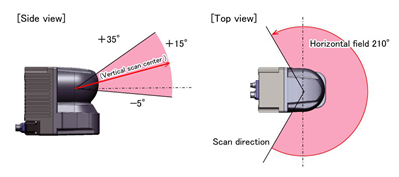
Sample 3D LiDAR and range (courtesy Hokuyo Automatic Co., LTD.)
What’s next for sensor technology?
Over the past decade, there have been significant advances in 3D sensor technologies and methodologies.
From optical technologies that facilitate the integration of photogrammetry and augmented reality to new solid-state and flash LiDAR’s, modern technology is enabling faster scanning, higher resolution (accuracy), smaller sensors, and cheaper prices.
We see this everyday on things such as our mobile phones and Google Maps. However, once these terrestrial sensors are placed in a corrosive, GPS-denied environment — such as a sewer — the time and algorithms required to produce meaningful information is inherently longer and more expensive. The simultaneous localization and mapping (SLAM) of our deteriorated buried infrastructure is a computational problem that has yet to be solved on scale.
In the coming years, I would expect inspection sensors and technologies to become more standardized, easier to deploy, more accurate, and better able to produce the same types of deliverables that we see from our above-ground counterparts.
Which is best for your pipeline assessment?
Now that you understand the differences between 2D and 3D sensors, you’re probably wondering which is best for your pipeline inspection.
At RedZone Robotics, we’ve been conducting advanced pipeline assessments and sewer inspections for over 20 years for organizations around the world. Our goal is to get you the most comprehensive, actionable data so that you can confidently make critical decisions about your underground infrastructure.
We use autonomous robot technology, built by our in-house engineers, along with secure, proprietary asset management software to help you analyze and properly maintain your pipeline.
Ready to learn more? Complete the form below to schedule a demo, consultation, and/or inspection today!
Ready to get started? Connect with us today!
Complete this form to schedule your next advanced pipeline assessment & sewer inspection, get a quote, or connect with a RedZone Robotics team member.
Want to know how RedZone Robotics helps you to reduce your CARBON BOOTPRINT? Click here to learn more!