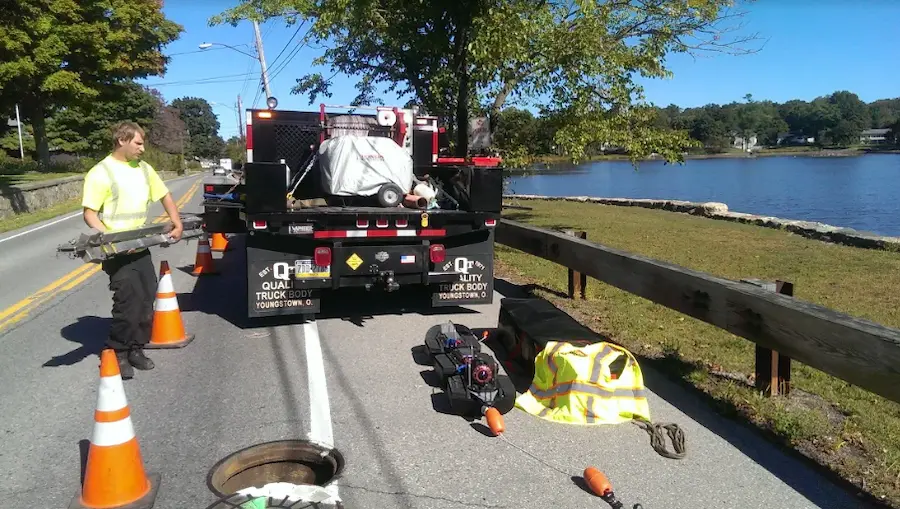
Accurately assessing large-diameter, underground infrastructure was historically a dangerous job left to those game enough to trudge through the sewer or float down on a surfboard with their rock hammer, cover meter, or measuring bar in tow. With the increased logistics and requirements around health and safety, high-risk manned entry inspections have increased in cost and complexity. Technology advancements provide not only a replacement, but a survey that encompasses every inch of the lines in question.
Designing for Safety and Cost Effectiveness
The Profiler suite of products were developed to replace manned walk-throughs and provide accurate cost effective solutions that did not require expensive bypass pumping or diversions. The original large-diameter Profiler tool, dubbed the 33, was developed over a 5 year period. During this time, it shrunk from a unit that was over 15 feet long and required assembly within the pipeline, to a floating platform that could be deployed from any access point. Then the unit morphed into the commercially available HDProfiler, first deployed in the United States in 2009. The Profiler system provided not only a visual inspection of the pipeline, but also a synchronized laser and sonar measurement. These tools provided the full quantitative cross-section of the state of the pipes. Detailed analysis using machine vision highlighted and measured areas of corrosion, ovality, brick loss and sediment build up both above and below the flow.

Profiler’s ability to capture long stretches of data from a single deployment allowed the unit to stand out from its competitors. During one of the first deployments of the HDProfiler, the unit was successfully able to investigate a pipeline over 15,0000 feet from a single access point. The combination of battery power, onboard data logging, and strobing lights removed the requirement of expensive and specialized fiber cables that had hampered remote investigation of long sewer tunnels and allowed the inspections of many that had never before been inspected.
Profiler Downsizes: From 36 inch to 20 inch Pipe
The original HDProfiler unit was designed to start inspecting pipelines from 36 inches and upwards. Interaction with experienced city engineers, especially in smaller municipalities, brought about the realization that we needed to shrink the technology to allow inspections starting at 20 inches. This opened up the advantages of this type of data to a larger group of cities. As a result of this insight and customer feedback, the MD Profiler was developed.
MD Profiler utilized the same concepts as it’s predecessor, however technological advancements allowed field crews to run all three data streams on a single computer, drastically shrinking the payload required to be transported beneath the ground. The MDSystem was successfully first deployed in the closing months of 2012.
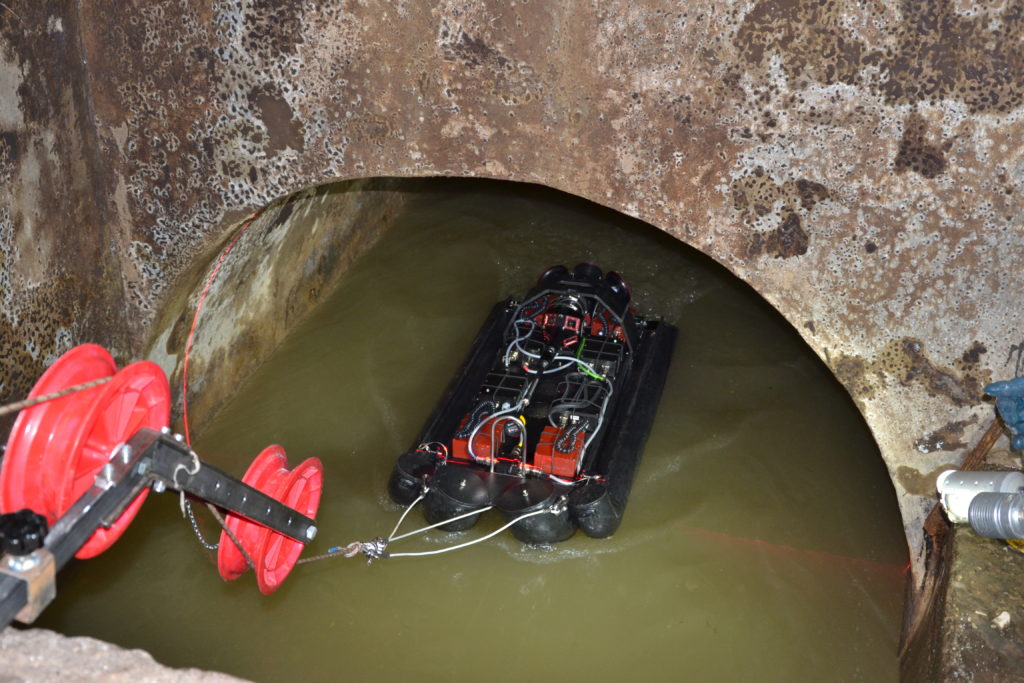
The newer generation cameras and computers, coupled with the underground operating software developed with the MDSystem was then repurposed to replace the HDProfiler with the 2nd generation SMD Profiler, allowing crews flexibility in the field to capture pipes from 20” up to 125” with one suite of equipment. This resulted in a streamlined on-site experience. The move to a singular onboard computer allowed additional space to increase the battery life of the system to over 8 hours, ensuring successful data collection in even the longest, most difficult to access pipelines.
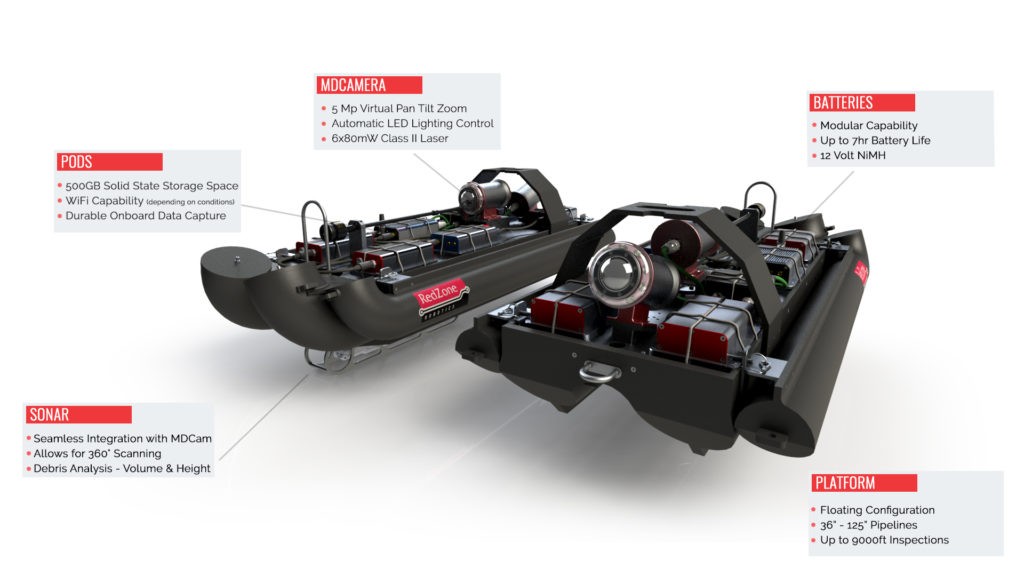
The significant advantage of quantifying the condition of the pipelines, coupled with the reach and ease of deployment has since seen the 3 generations of Profiler units collect over 10.5 million feet around the world, providing engineers and city officials critical insight into the state of their underground infrastructure. The information collected by the units, and the reports created from them, allow data driven decisions to be made successfully, saving cities millions of dollars.