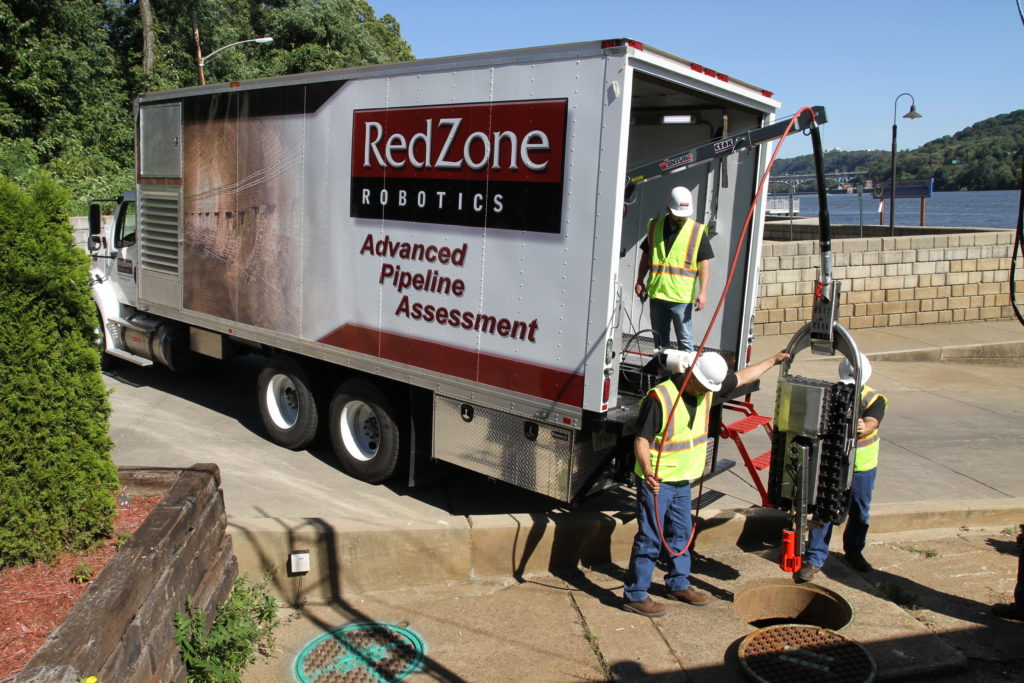
As U.S. infrastructure rapidly ages, organizations have shifted focus to assets that are often out of sight and out of mind – buried linear assets.
These pipes and tunnels are among some of the oldest structures in America, dating back to the 1800s, and have fallen into disrepair due to neglect, increased or unintended use, and many other variables. If you’re like most other system owners, you’ve implemented routine condition assessments using CCTV and defect rating systems to determine the deterioration and deficiencies of these pipes.
These improved inspection methods, specifically those for large-diameter pipes, offer clearer data and solutions. So, what sort of data do you actually get, and how?
In this article, we’ll break down the advantages of a multi-sensor inspection (MSI) for your large-diameter pipes.
Not all pipes are alike
One of the key distinctions for linear assets is diameter (pipe size).
Estimates place 75% or more of the pipes in a conveyance system to be 12 inches or less, resulting in an abundance of pipe to be reasonably accessible and capable of inspection with standard equipment.
But what about remaining 25% of systems? And, what exactly is a large-diameter pipe, and how do you inspect it?
Large-diameter pipe has been classified as anything greater than 15 inches in diameter. For you. and other system owners alike, the classification of large-diameter pipe may vary. For example, not every system requires 60 inch pipes, but in some metropolitan areas, that size might not be adequate.
Typically, these larger lines are classified as trunk or interceptor pipes. These linear assets are designed to convey flow from smaller lines that feed it, to one central location.
As the pipes get bigger, they are required to maintain more hydraulic capacity. This often results in higher and faster flows, as well as other hazardous conditions, such as sediment buildup and hydrogen sulfide gas (H2S).
Performing an assessment on the condition requires nothing but the strongest and most capable machinery for navigating and collecting this inspection information.
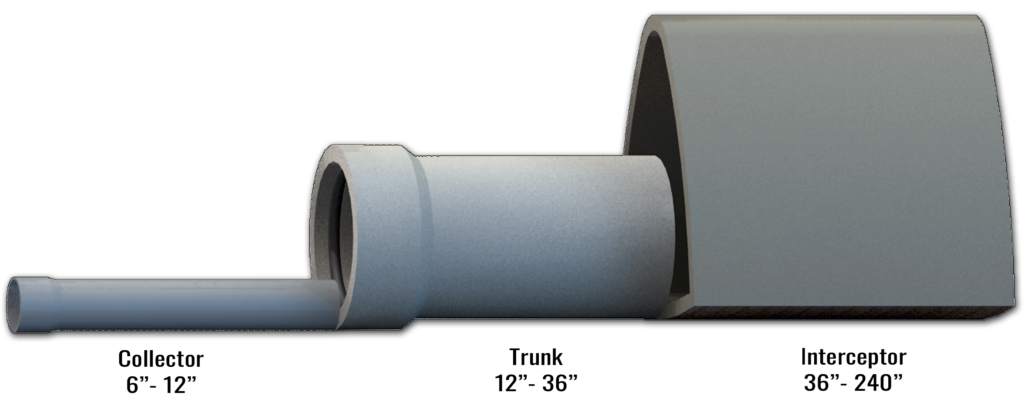
RedZone’s Responder® to the rescue
Enter Responder®.
Weighing in at over 700lbs, this hydraulic-tracked, independently-steered, robotic crawler was designed for handling varying conditions. It’s also capable of inspecting 36-inch to 240-inch diameter pipes, and larger.
Due to its incredibly capable cable and winch system, it can successfully traverse 4,000 linear feet of distance in one deployment. This ensures reduced traffic control and public disruption from inspection activities.
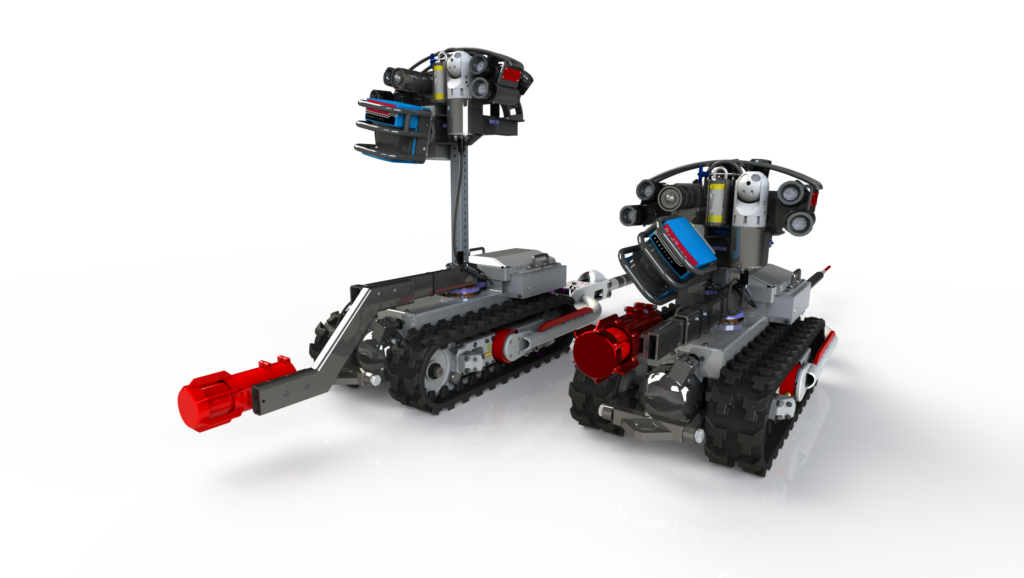
Equipped with a 1080p HD lens, Responder® allows for a full 360-degree view of the interior of the pipeline, complete with pan/tilt/zoom navigation. While CCTV is the backbone of inspection, it can’t provide the full picture, like Responder® can.
Multi-sensor inspection for healthier pipes
Typically, pipeline inspection involves flow.
Unfortunately, standard CCTV inspections beneath wastewater don’t provide the clearest image quality. While those units can zoom for long distances above the flow, they don’t provide clear enough imaging to figure out how much material has deteriorated from the pipe walls.
That’s where a multi-sensor inspection (MSI) truly shines. With Responder®, you’ll get quantifiable results by utilizing sonar, LiDAR, and gas detection.
How sonar works during a multi-sensor inspection
Sonar uses audio pulses below the flow to detect the echo, or return of that audio, off of a surface.
The time taken from emitting the pulse to receiving the echo provides a distance measurement. When you analyze and compare these readings to the expected diameter of the pipeline, you’ll be able to calculate debris measurements such as depth and volume.
You can then use that information to determine not only hydraulic capacity loss, but also cleaning regimen, including how much debris may need to be removed prior to a rehabilitation project.
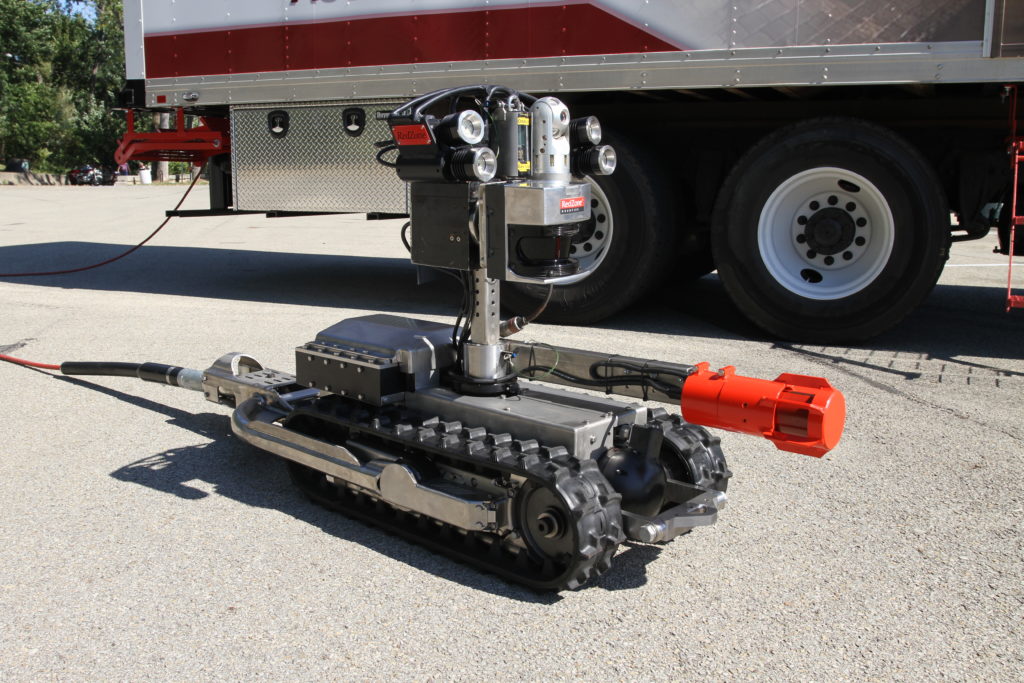
How LiDAR works during a multi-sensor inspection
The LiDAR sensor works via a time-of-flight principle (ToF), and similar to sonar, measures the return of a light pulse off of a surface.
This produces detailed, high-accuracy, three-dimensional (3D) scans of the interior wall of the pipe. It also allows for comprehensive reporting of the internal condition.
Cross-sections of the laser return are compared to the expected diameter. This enables Responder® to gather corrosion (where the cross-section is larger than the expected diameter) or buildup (where the cross-section is smaller than the expected diameter) measurements.
Additionally, in flexible materials, this can be used to measure the ovality of the pipeline.
Analyzing the Data
From the Responder®’s 3D scans, full-detail models of the entire pipe, from access point to access point, can be constructed and utilized for determining alignment.
Because these pipes are below ground, it can be difficult to determine where one might bend or curve in relation to above-ground infrastructure, such as streets or buildings. In rehabilitation design, this alignment can be used for measuring the curvature of the bends. It can also be used for sliplining and mandrel testing.
Sliplining is a common method for extending the useful life of a linear asset. The design process involves not only determining the current internal diameter (cross-section) of the host pipe, but what lengths of the new pipe can fit around the bends.
Typically, this is done by dragging or pushing a mandrel (a manufactured piece of steel, measured to a specific diameter to simulate replacement pipe) through the host pipe. By performing this step virtually via LiDAR scans, you’ll save a significant amount of money, and limit potential damage to the host pipe.
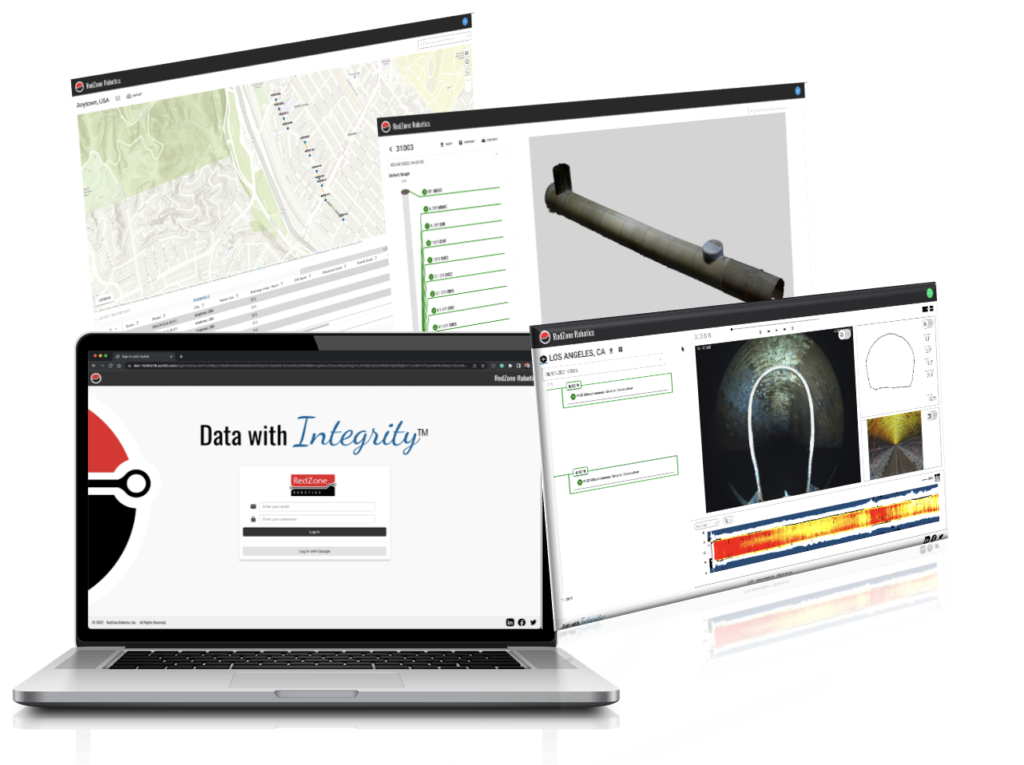
So, where do you store the pipeline data once you’ve got it?
Once you’ve obtained actionable data from your multi-sensor inspection, you’ll need a secure, easy-to-access storage solution.
Data storage allows you to review your assets over time to create better maintenance schedules, and to determine deterioration. At RedZone Robotics, we use our own proprietary, cloud-based platform – Integrity®.
Within it, you’ll have access to some of the most advanced video and imagery. You’ll also have the ability to manipulate crystal-clear 3D models of your assets, and view your entire system via ESRI -based mapping tools. You can even zero in on specific assets based on their NASSCO defect scoring, and export condition reports with the click of a button.
While gathering pipeline data is important, the way you use and store it is vital to your system’s overall health.
Bringing it all together
Large-diameter pipelines are not only complicated infrastructure, but they can be difficult to assess.
CCTV inspections provide important information. However, a multi-sensor inspection gathers information that you just can’t get above the flow. When you use a tool such as Responder® to complete that inspection, your data becomes actionable. And, because it’s unmanned technology, you won’t put your team in harm’s way by sending them into the pipe.
The expertise of RedZone Robotics team members, along with the advanced technology of the Responder® unit can streamline the work. We’re here to help you meet your objectives while removing the undue stress and burden of asset management.
Ready to schedule your multi-sensor inspection? Maybe you’d like to get a demo or quote first? Just complete the form below to get started!